
Embracing Neurodiversity at the Workplace
31/08/2023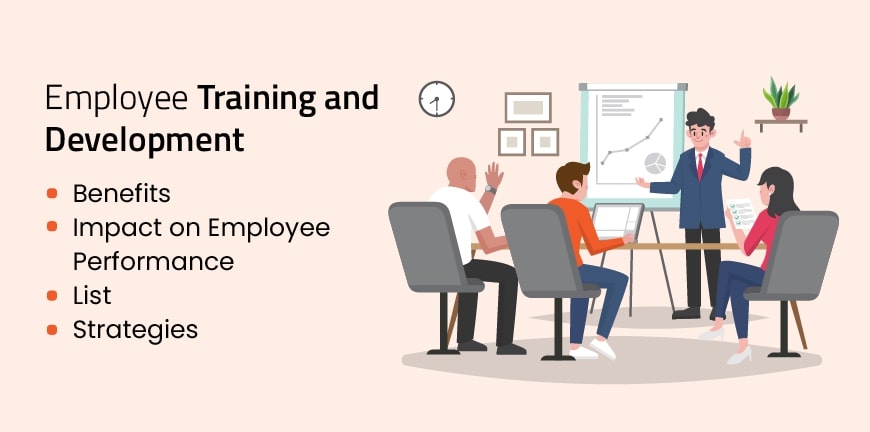
What is Employee Training and Development?
04/09/2023One can argue that the manufacturing industry is at the heart of all industry. Statutory compliance in the manufacturing industry is crucial to the safety of its workers, the quality of the products and services delivered and to the reputation of the company itself.
The Government cares for employee welfare but also wants organisations to succeed. For this, the Government statutory schemes are those schemes that are instituted by the government to guarantee employee health and safety. These include the provisions made under enactments such as the Factories Act 1948, the Mines Act 1962 etc.
If you are a manufacturing company, then you must have a statutory compliance checklist in accordance with the Factories Act of 1948 amended in several amendments since then; one that you follow regularly and adhere to without exception. But what exactly is statutory or regulatory compliance in the manufacturing industry?
What is Statutory Compliance for Manufacturing Industry?
Statutory compliance in HR refers to the efforts made by a company to comply with labour laws and regulations set by the state and central governments. In the context of the manufacturing industry too, there is statutory compliance that companies must follow for the sake of employee welfare and to keep the brand reputation intact.
In the case of statutory compliance for the manufacturing industry, it is possible that in certain domains such as minimum wage laws only directives from specific state governments exist whereas other domains may have both state and central laws.
Statutory Compliance Issues in Manufacturing
There are several issues in statutory compliance possible on the industrial floor. Many of these statutory or regulatory compliance issues can seriously hamper the functioning of the enterprise. Let us look at some of the common issues now:
Lack of minimum age and qualification for work
Child labour is a rampant problem in India. Several factories still employ children in their factories. This is especially the case in the unorganized sector, but it is possible in other factories too. Organisations are looking at ways of cheap labour through apprentices. Though apprentices are eligible to work on the factory floor, they too have some minimum requirements such as a fifth-grade qualification and other skill requirements.
Lack of minimum wages
Workers in the factories in many parts of India are underpaid and not even offered minimum wages. The state governments have fixed minimum wages which must be followed in each state but not everyone abides by it. Not paying minimum wages can lead to employee mistrust and risk of interventions from labour unions, low engagement levels and lower productivity levels.
Working beyond work hours
Working beyond the 9 hours of work stipulated by the government for a day is unfortunately a norm in many factories across India. When people are overworked, their stress levels increase, errors in production also lead to product quality issues which will eventually lead to customer dissatisfaction. If workers are working overtime, then they must be paid overtime pro rata, failing which the company does not follow statutory compliance.
Lack of work safety and hazard protection
The Occupational Safety and Hazard Management Code (OSH) stipulates that workers can have an open discussion with their floor supervisors on safety conditions and that they must be informed of the potential risks of employment and other hazards on the floor before they begin the work. Workers must also be offered sufficient compensation in the case of accidents under the provisions of the code.
Statutory Compliance Checklist for Manufacturing Companies
The legal statutory compliance checklist for manufacturing companies includes several points that companies must adhere to. Let us look at some of these points now.
Health
- The factory floors, walls, vents and other fixtures must be cleaned and maintained well to prevent spread of disease.
- Disposal of waste must happen through proper methods and workers must wear gloves and other safety accessories when handling waste.
- There must be sufficient ventilation and a proper temperature in the factory to ensure that the health of the workers is not affected.
- Avoid overcrowding on the factory floor or elsewhere to reduce the risk of hazards.
- Ensure that the areas are well-lit to prevent any hazards
- Sufficient drinking water must be provided, especially to prevent the risk of dehydration in the summer months.
- The toilets must be easily accessible to workers
- First aid and medical facilities must be within reach in case of any emergency
Safety
- Train people for operating the machinery safely and conduct several drills
- The machines should be maintained well to prevent any hazards
- Ensure that workers do not undertake any work that will most certainly risk their health
- Ensure that there is no leakage of poisonous gases and fumes
- The factory should prevent the outbreak of fire
Welfare
- Facility must be provided for sitting and relaxing when they are tired
- Canteen must be present adjacent to the factory and must be clean and hygienic
- Welfare officers must be present on the floor to ensure that workers’ rights are not violated
Work Hours
- Workers should not work in a factory for more than 48 hours
- Workers must not work for more than 9 days without a holiday
- If the weekly holidays are not adhered to, then workers must be offered a leave in the same month
- Workers must not work for more than 9 hours a day
- Workers should be paid pro rata for working overtime
Looking for Statutory Compliance Assistance?
A safe workplace (in this instance, a safe factory) is a result of not only aligning the workplace policies with the laws and regulations laid down by the government but also securing the cooperation of the employees in making it happen. This could be a balancing act not all companies are necessarily prepared for, and it not only costs additional resources but takes away from the time that can be spent on other strategic activities.
Did you know for instance that you could recruit apprentices under the NAPS Act of 2016 for your factories, but that they should meet certain minimum requirements for age and skill levels. Did you also know that you are eligible for reimbursement from the government during both their training and work on the factory floor under NAPS?
Alp Consulting can partner with you in your NAPS journey and to ensure statutory compliance on the factory floor and even help you manage your payroll effectively. As an HR consulting company with over 25 years of experience, you can count on us to manage all functions of HR for you, right from recruitment and staffing to payroll and compliance. When are you talking to us, and how can we help?